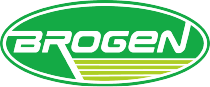
Brogen
- Email:inquiry@brogenmotors.com
- Whatsapp:+86 19352135902
- Wechat:Brogenmotors_SH
- Tel:+86 19352135902
Brogen
1. Requirements Analysis: First, we conduct a detailed technical requirements analysis for buses of different lengths, understanding factors such as passenger capacity, expected range, vehicle weight, and spatial layout.
2. Battery Pack Capacity Design: Based on the specific needs of each bus model, we design battery packs of different capacities. For example, an 8-meter bus might require a smaller battery pack to accommodate its smaller passenger capacity and weight, while a 12-meter bus might need a larger battery pack for longer range requirements.
3. Space Optimization: Considering the space limitations inside the bus, we optimize the use of space when designing the battery pack to ensure it meets energy requirements while fitting the vehicle's structural layout. Different types of electric buses have significant variations in the placement of batteries, with some installed on the roof, some at the rear, and others at the bottom. We need to make reasonable design adjustments based on the structural differences of the buses.
4. Modular Design: We use a modular design approach, allowing the number of battery cells in the pack to be increased or decreased as needed to suit the requirements of buses of different lengths. This way, even with different voltage and current requirements, the number of battery cells can be adjusted to fit.
5. Voltage and Current Adaptation: We design a specialized Battery Management System (BMS) to adapt to different voltage requirement, ensuring the battery pack can provide sufficient power while remaining safe and stable.
6. Compatibility Testing: We conduct extensive compatibility testing during the design phase to ensure the battery pack can operate normally on buses of different lengths and under various driving conditions.
7. Technical Communication and Collaboration: Maintain close technical communication with clients to ensure the design meets their specific needs and to address any technical issues promptly during development. 8. Continuous Iteration: Continuously optimize the battery pack design based on test results and client feedback to ensure the final product meets all technical specifications and performance requirements.
At Brogen, we're committed to offering custom EV solutions. We back these with new technologies to help EV companies thrive and promote environmental sustainability. Brogen provides an industry-leading EV Powertrain solution for commercial vehicles.
We've forged strategic alliances with key players in the new energy vehicle sector, including electric motor and controller manufacturers, battery pack producers, and charging station suppliers. We also collaborate with suppliers of essential components such as EV car battery, electric vehicle motor(PMSM motor), motor controller, OBC+DCDC+PDU, axial flux motor, BMS, air conditioning systems, air compressors, and power steering systems.
We have delivered high-quality electric powertrain solutions to over 100 customers across more than 20 countries.
Get in Touch with Our Experts
Are you interested in empowering your EV project? Reach out to our experts at inquiry@brogenmotors.com. We promise to get back to you within two business days.
For more videos please click Brogen’s Youtube.
For the latest news please view Brogen’s Linkedin.
Connect with a Brogen expert to learn more about our services and discuss our ePowertrain solutions.
Product Manual