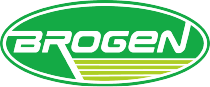
Brogen
- Email:inquiry@brogenmotors.com
- Whatsapp:+86 19352135902
- Wechat:Brogenmotors_SH
- Tel:+86 19352135902
Brogen
The traditional drive axle is located at the end of the transmission system, and its main function is to decelerate and increase the torque of the power coming from the transmission, and transfer the power to the drive wheels. However, with the continuous progress of motor technology, the performance of drive motors has been significantly improved, and the role of ordinary rear axle in decelerating and increasing torque has been gradually weakened. Therefore, electric drive axle technology has emerged and is becoming an important trend in the future development of electric vehicles.
The central integrated electric drive axle has become the mainstream in the current market due to its high integration, high transmission efficiency, mature technology, easy maintenance and other advantages. The integrated electric drive axle is mainly divided into three types: parallel-axis type, same-axis type and vertical-axis type according to the arrangement of motor and drive axle.
Vertical-axis electric drive axle due to structural problems, compared with the same-axis and parallel-axis electric drive axle performance is inferior. Parallel-axis electric drive axles and coaxial electric drive axles have their own advantages.
Structural characteristics: The motor and the output half-shaft of the drive axle are arranged in parallel, and the motor is usually placed on one side.
Structural characteristics: The motor and the output half-shaft of the drive axle are arranged coaxially.
Coaxial electric drive axle | Parallel-Axis Electric Drive Axle | |
Compactness | Highly integrated, compact structure, small size, easy to arrange for the whole vehicle. | Relatively decentralised structure, but compact arrangement can be achieved through optimised design. |
Transmission efficiency | Short transmission path, high efficiency, reduced energy loss. | Higher efficiency, but may be slightly lower than coaxial electric drive axle. |
NVH performance | Better NVH performance due to compactness. | NVH performance is also good, but relatively difficult to optimise. |
Cost | Higher development and manufacturing costs, but cost-effective in the long run. | Lower cost, mature technology, simple processing and manufacturing. |
Weight | Lighter weight with lightweight design. | Relatively light weight, but may not be as light as coaxial electric drive bridges. |
Maintenance | Relatively complex to maintain, but highly reliable. | Easy to maintain, as the motor and reducer can be dismantled separately. |
Coaxial electric drive axle and parallel-axis electric drive axle each has its advantages and disadvantages, in practical applications of the two electric drive axle programme are more desirable, the final choice of which type of electric drive axle needs to be based on the specific needs, application scenarios, and cost and other factors for comprehensive consideration. So you think the centralised electric drive axle design, the future will be towards that trend and direction?
For more information about electric axle systems for commercial vehicle please click Brogen Electric Axle.
Are you interested in empowering your EV project? Reach out to our experts at inquiry@brogenmotors.com. We promise to get back to you within two business days. For more videos please click Brogen’s Youtube. For the latest news please view Brogen’s Linkedin. Please note that our products are not ready-made or plug-and-play type. Depending on customers' different requirements, it may involves many customizations and modifications. For further discussion please contact us.
Connect with a Brogen expert to learn more about our services and discuss our ePowertrain solutions.
Product Manual