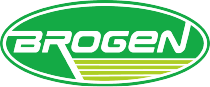
Brogen
- Email:inquiry@brogenmotors.com
- Whatsapp:+86 19352135902
- Wechat:Brogenmotors_SH
- Tel:+86 19352135902
Brogen
Currently, the main electric drive types of pure electric commercial vehicles are central direct drive and electric axles. Central drive replaces the engine with a drive motor, and still uses the traditional fuel vehicle configuration; electric drive axles integrate the drive motor and transmission into the axle.
In harsh scenarios such as heavy loads and unpaved roads, central drive with traditional drive axles dominates. For trunk highway logistics, sanitation and other scenarios, electric drive axles with higher integration and efficiency are the future development direction. At present, the market share of electric drive axles has gradually expanded, and has been widely used in light trucks of 4.5 tons and below.
The first generation of wheel-side electric drive axles has been eliminated due to the longitudinal motor and vertical shaft transmission; the hub electric drive axle has an inner rotor hub motor structure.
The electric drive axle eliminates the drive shaft, shortens the drive chain, and improves system efficiency; reduces the curb weight of the vehicle; the battery can be installed on the inside of the frame, improves safety, increases the battery installation position and saves truck loading space.
Electric drive axle technology continues to develop, and has undergone three generations of changes in integration.
The first generation of electric drive axles: based on the transformation of traditional bridge shells, using water-cooled round wire motors, single motors are separately mounted, pneumatic or electric shifting, and power interruption during shifting.
The second generation of electric drive axle: adopts segmented combined axle housing, oil-cooled flat wire motor, integrated design of motor and transmission, electric shifting, and no power interruption during shifting.
The third generation of electric drive axle: has the characteristics of segmented combined axle housing, integrated motor controller, distributed drive, coaxial motor, etc.
Use high-speed motor and high-speed transmission to reduce motor torque, increase gearbox ratio, and reduce assembly weight. Expand the motor high efficiency area and improve energy utilization efficiency. Develop from low-speed motor to medium-speed motor and then to high-speed motor, pursuing high reliability, high efficiency, high speed and low cost. Highway transport vehicles require large reserve power and have developed towards 600kW; the total power required for engineering and mining vehicles is relatively small. The motor speed continues to increase, and flat wire oil-cooled motor has become the development trend of drive motor for electric drive axle.
Adopt flat wire technology to increase the stator slot full rate, reduce the height of the winding end, improve space utilization, and reduce the weight of the motor under the same parameters. Flat wire motors have an absolute advantage in improving slot fill rate, with a larger high-efficiency zone area, an efficiency increase of 1.5%, and a loss reduction from 4.5% to 3%. Compared with round wire motors, they have obvious improvements in material cost, power density, weight, high-efficiency zone, winding temperature rise, NVH (noise, vibration and harshness), etc.
Use oil-cooled motors to improve the power density and torque density of the effective part of the motor. Oil-cooled motors can dissipate motor heat more directly, shorten the cooling path, and cool all parts. They have obvious advantages in the motor cooling system and have become the preferred cooling method for high-performance motors in the industry. Compared with water cooling, they can effectively avoid local overheating problems.
The electric drive axle can be modularly combined with systems and components. The power of a 4.5-ton truck is 70/140kW×1, the power of an 18-ton truck is 140/280kW×2, the power of a 25-ton truck is 210/420kW×3, and the power of a truck of 49 tons and above is 280/560kW×4.
The rotor strength design has a great impact on motor performance. Because the electric drive axle is directly impacted by the high load of the tire, the motor, as an unsprung component, is subject to greater vibration impact. If the rotor is not strong enough, problems such as excessive magnetic bridge stress or even breakage may occur when rotating at high speed, which will directly affect the reliability and stability of the motor, and thus affect its performance indicators such as power output and speed.
If you need to electrify your engineering fleet, please contact us. We will provide a suitable solution for you. Reach out to our experts at inquiry@brogenmotors.com. We promise to get back to you within two business days.
Brogen is a leading ev solutions provider for commercial vehicles. You can find more ev solutions in our website, for example, electric vehicle powertrain solution, battery solution, and electric axle systems. Beside that, we have the cutting-edge axial flux motors for Automakers, who pursue excellent engine performance. We are proud to serve as your one-stop solution for navigating the rapidly expanding electric vehicle (EV) market.
For more videos please click Brogen’s Youtube. For the latest news please view Brogen’s Linkedin. Please note that our products are not ready-made or plug-and-play type. Depending on customers' different requirements, it may involves many customizations and modifications.
Connect with a Brogen expert to learn more about our services and discuss our ePowertrain solutions.
Product Manual