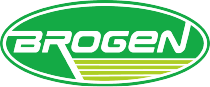
Brogen
- Email:inquiry@brogenmotors.com
- Whatsapp:+86 19352135902
- Wechat:Brogenmotors_SH
- Tel:+86 19352135902
Brogen
Porsche's first all-electric sports car, the Taycan, showcases numerous innovations, including its Hair-pin motor—a technology poised to lead the next generation of electric drive systems. At the Frankfurt Motor Show, Great Wall Motors and Schaeffler, among others, exhibited the prowess of their Hair-pin motors. But why is this technology considered the "key" to ushering in a new era of electric drive?
The Hair-pin motor is distinguished from traditional "round wire motors" by the shape of the stator windings. While traditional motors use round wires, Hair-pin motors employ flat, rectangular ones.
The evolution of new energy vehicle drive systems is trending towards miniaturization, integration, and high power density. Hair-pin motors excel in these areas, offering compactness, material efficiency, and enhanced power.
Under the WLTC (World Light Vehicle Test Procedure) standard working conditions, the conversion efficiency of the flat wire motor is 1.12% higher than that of the traditional round wire motor; under the global average, the efficiency values of the two differ by 2%; under urban working conditions (low speed and high torque), the efficiency values of the two differ by 10%.
Motor Efficiency | Average Efficiency (WLTC) | Average Efficiency (full speed) |
Hair-pin Motor | 92.49% | 94,78% |
Round Wire Motor | 91.37% | 92.76% |
Difference | 1.12% | 2.02% |
The Hair-pin motor's higher slot fill rate—due to the compact nature of Hair-pins compared to the gaps between round wires—translates to a stronger magnetic field and greater motor power. Data indicates that Hair-pin motors can accommodate 20-30% more wires in the same space, effectively boosting power by a similar margin. This also means a more compact motor can achieve the same power density.
The current level of round wire motors is about 3.5kW/kg, while the power density of hair pin motors of current leading companies is about 4.5kW/kg.
The Hair-pin design also enhances heat dissipation due to increased wire contact area and reduces consumables due to the smaller winding volume. This translates to better acceleration performance and reduced noise, significantly improving overall vehicle performance.
Despite its advantages, the Hair-pin motor faces challenges such as design and manufacturing complexities, and increased wear. The industrialization of Hair-pin motors is hindered by raw material, process, and equipment hurdles, which contribute to their limited widespread adoption.
The transition from round to flat rectangular wires also necessitates innovation in upstream wire manufacturing technology. The absence of cost-sharing partners before market maturity results in high R&D costs for car companies.
In summary, while Hair-pin motors are not yet a dominant force in replacing traditional motors, the inherent risks of short-term production and application are currently too significant for car companies to embrace. The journey from lab to market is fraught with challenges. However, technological evolution is an inevitable trend, and Hair-pin motors are likely to play a pivotal role in the future of new energy vehicles.
Connect with a Brogen expert to learn more about our services and discuss our ePowertrain solutions.
Product Manual