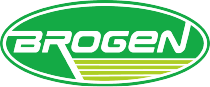
Brogen
- Email:inquiry@brogenmotors.com
- Whatsapp:+86 19352135902
- Wechat:Brogenmotors_SH
- Tel:+86 19352135902
Brogen
A hairpin motor, also known as a flat wire motor, is an electric motor that utilizes rectangular copper wires (hairpin windings) instead of traditional round wires. This design features a stator and rotor, with hairpin-shaped conductors welded together to form the stator windings. Initially developed for high-power industrial applications like generators and heavy machinery, hairpin motors have become a cornerstone of modern electric vehicles (EVs), powering drivetrains, steering systems, and auxiliary components.
Hairpin motors are classified by their winding configurations:
Hairpin Winding (most common): Shaped like hairpins, these conductors are inserted into stator slots and welded at one end. They offer high slot fill rates (up to 75%) and excellent thermal conductivity.
X-Pin Winding: Optimized for faster welding processes, X-pins reduce heat-affected zones and improve production efficiency.
S-Winding: A variation of hairpin winding that enhances compactness and power density.
Rectangular wires fill stator slots more efficiently (70-75% vs. 40-50% for round wires), enabling 20-30% more power in the same volume. Example: A 200kW hairpin motor can be 15% smaller than a comparable round wire motor.
Larger surface area of flat wires improves heat dissipation by up to 25%, reducing the need for complex cooling systems. Critical for high-performance EVs, where overheating can degrade battery life.
Lower resistance and reduced AC losses (skin effect mitigation) boost efficiency by 3-5%, extending driving range in EVs.
Uniform magnetic field distribution minimizes electromagnetic noise, enhancing NVH (Noise, Vibration, Harshness) performance.
The thick copper wire of the flat wire motor has a certain elasticity, and there will be a certain degree of rebound after bending. The insulation layer will also become more easily damaged due to bending and rebound, resulting in gaps. Therefore, a deformation margin must be left during design, which is more difficult.
When there is alternating current or alternating electromagnetic field in the conductor, the current distribution inside the conductor is uneven, and the current tends to concentrate on the "skin" part of the conductor surface. This is the so-called "skin" effect. The result of this effect is that the resistance of the conductor increases, and the loss power of the conductor also increases accordingly. The trend of new energy vehicle motors tends to be high power and high speed. The specific manifestation in flat wire motors is that when the frequency is higher, the AC copper loss of the flat wire winding will be higher.
Due to the complex process and high precision requirements of flat wire, the initial investment in production is very large. If its precision is not high, the reliability and consistency of the product will be relatively poor. It is basically impossible to achieve large-scale mass production through manual manufacturing, and professional high-end equipment must be relied on.
The main disadvantage of flat wire motors is that it is difficult to achieve very dense serial design, that is, it is not flexible enough, so it is a great challenge for motor designers. From the perspective of designing motors, a set of solutions are generally designed to expand a series of different designs.
If only a 100KW motor is needed, but when designing, a series of motors in the range of 80-120KW need to be designed, one is to meet potential needs, and the other is to open up the design differences with other companies.
Flat wire conductor, each coil has 1 turn, and two adjacent coils are connected in series by welding; when the number of parallel branches is constant, the only way to change the number of motor turns is to adjust the number of pole slots and the number of conductors per slot; the adjustability of flat wire motors at different power levels in the design is worse than that of traditional round copper wire motors, and the overall optimization and matching design of the top layer of the electric drive system platform is required.
For round wire motors, the core and the number of slots are the same, but the length and the number of turns of the coil are different, so it is relatively easy to design a series. However, it is difficult for flat wire motors to achieve this effect. Because the number of turns of flat wire motors is relatively small, reducing one or two wires will have a greater impact on the performance of the entire motor.
Hairpin motors represent a paradigm shift in electric motor technology, offering unparalleled efficiency, compactness, and reliability. As EV adoption accelerates and industrial automation advances, hairpin motors will play a pivotal role in shaping a greener, more energy-efficient future.
If you need to electrify your engineering fleet, please contact us. We will provide a suitable solution for you. Reach out to our experts at inquiry@brogenmotors.com. We promise to get back to you within two business days.
Brogen is a leading ev solutions provider for commercial vehicles. You can find more ev solutions in our website, for example, electric vehicle powertrain solution, battery solution, and electric axle systems. Beside that, we have the cutting-edge axial flux motors for Automakers, who pursue excellent engine performance. We are proud to serve as your one-stop solution for navigating the rapidly expanding electric vehicle (EV) market.
For more videos please click Brogen’s Youtube. For the latest news please view Brogen’s Linkedin. Please note that our products are not ready-made or plug-and-play type. Depending on customers' different requirements, it may involves many customizations and modifications.
Connect with a Brogen expert to learn more about our services and discuss our ePowertrain solutions.
Company Profile