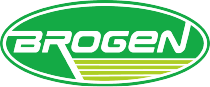
Brogen
- Email:inquiry@brogenmotors.com
- Whatsapp:+86 19352135902
- Wechat:Brogenmotors_SH
- Tel:+86 19352135902
Brogen
Due The electric drive system is one of the three core systems of electric vehicles and serves as the primary propulsion system. Its characteristics are pivotal in determining the vehicle's key performance indicators, directly influencing its power, efficiency, and the overall driving experience.
The term "three-in-one" (3 in 1) refers to the integration of electric motor, motor controller, and the reducer into a single unit. This integration aims to reduce weight and volume while increasing power and torque density. It also offers significant benefits in terms of NVH (Noise, Vibration, and Harshness) and EMC (Electromagnetic Compatibility). From a power and economy perspective, this integration is considered a significant advantage.
As electric vehicle technology continues to develop, the trend towards integrated design is expected to shape the future of development.
The three-in-one electric drive system comprises a drive motor, a motor controller (MCU), and a reducer (Gear Box). These components are interconnected with the vehicle's other systems through high and low voltage wiring harnesses and cooling pipes.
The development of the electric drive system is guided by the requirements set by the vehicle as a whole. Key development goals include:
Brogen supplies premium 3 in 1 powertrain system for heavy-duty trucks. Below is product's picture and its specifications.
Item | Parameters | |
Motor | DC voltage platform (V) | 637 |
Rated/Peak power (kw) | 200/300 | |
Rated torque (N.m) | 1300 | |
Rated/Peak speed (rpm) | 1469/2800 | |
Protection level | IP67 | |
Cooling form | Water Cooling | |
Motor Controller | Applicable motor type | Permanent magnet synchronous motor |
Applicable voltage range (VDC) | 400-750V | |
Rated voltage (VDC) | 637 | |
Rated/Peak capacity (KVA) | 233/406 | |
Low-voltage power supply input voltage range | 18-36V | |
Gearbox | Speed ratio | 8.507/4.943/2.994/1.876/1.216/1 |
Pneumatic shift pressure (bar) | 8-10 |
This approach reduces the complexity of the vehicle and its components, leading to cost savings. For instance, a car company might introduce an e-platform electric drive system with highly integrated components, offering a range of products to cater to different power needs and vehicle models.
This involves a transition from fully separated structures to shared housing for the motor and reducer, and eventually, to a shared housing for the motor, controller, and reducer. This design reduces part count, volume, and weight, thereby lowering costs.
High-speed motors can conserve expensive permanent magnet materials and reduce motor size, which is beneficial for enhancing power and torque density and reducing manufacturing costs.
The coaxial planetary gear system, compared to the parallel shaft gear system, offers advantages in compactness, which aids in maximizing system power and torque density.
The current solution for the three-in-one integrated electric drive system often involves a traditional single-speed two-stage reducer. However, a multi-speed transmission system can expand the motor's high-efficiency range, reduce energy consumption, and potentially increase driving range.
At Brogen, we're committed to offering custom EV solutions. We back these with new technologies to help EV companies thrive and promote environmental sustainability. Brogen provides an industry-leading EV Powertrain solution for commercial vehicles.
We've forged strategic alliances with key players in the new energy vehicle sector, including electric motor and controller manufacturers, battery pack producers, and charging station suppliers. We also collaborate with suppliers of essential components such as EV car battery, electric vehicle motor(PMSM motor), motor controller, OBC+DCDC+PDU, axial flux motor, BMS, air conditioning systems, air compressors, and power steering systems.
We have delivered high-quality electric powertrain solutions to over 100 customers across more than 20 countries.
Get in Touch with Our Experts
Are you interested in empowering your EV project? Reach out to our experts at inquiry@brogenmotors.com. We promise to get back to you within two business days.
For more videos please click Brogen’s Youtube.
For the latest news please view Brogen’s Linkedin.
Connect with a Brogen expert to learn more about our services and discuss our ePowertrain solutions.
Company Profile