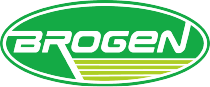
Brogen
- Email:inquiry@brogenmotors.com
- Whatsapp:+86 19352135902
- Wechat:Brogenmotors_SH
- Tel:+86 19352135902
Brogen
Axial flux motors, also known as "disk motors," differ from conventional radial flux motors in that their magnetic flux path is planar, with the air gap magnetic field direction parallel to the motor's axis.
The core technical advantage of axial flux motors lies in their structure, where the rotating rotor is positioned on the side of the stator (not inside the stator). This allows for a larger rotor diameter. Since torque is equal to force times radius, higher torque output can be achieved with the same force applied.
This means that, given the same amount of permanent magnet and copper wire materials, axial flux motors can achieve higher torque output. Unlike traditional radial flux motors, axial flux motors mainly include five key technologies.
Based on the number of stators and rotors, their relative positions, and the main magnetic path, the basic topological structures can be categorized into four types: single stator single rotor, double stators single rotor, single stator double rotor, and multi-disk structures. The selection of an appropriate structural topology should be assessed based on specific application scenarios, manufacturing processes, and cost factors. Currently, in the automotive electric drive industry, a comprehensive analysis of the performance, process feasibility, and cost of various types of axial flux motors is conducted, with a focus on adopting the double stator single rotor and single stator double rotor structures.
Traditional radial flux motors follow a nonlinear 2D magnetic flux path, whereas the new axial flux motors have a 3D magnetic flux path. Therefore, when performing performance simulation design, it is essential to consider the differences between the two and build models that enhance accuracy based on their respective characteristics.
For the new type of flux motor, a 3D multi-physics field joint simulation can be employed, along with a comprehensive optimization design of the electromagnetic scheme targeting multiple objectives. Continuously improve the computational efficiency of axial flux motor design and enhance the precision of virtual simulation capabilities, as illustrated in the 3D performance design of the axial flux motor.
For the development of stator frames, high-strength and high-insulation polyetheretherketone (PEEK materials, PEEK) are utilized;
For heat dissipation and cooling, high-strength and high-thermal-conductivity epoxy resin encapsulation and filling materials are developed to enhance the heat dissipation capability of the motor body and prevent the demagnetization of permanent magnets at high temperatures. As shown in below, the stator windings of the axial flux motor are encapsulated with epoxy resin;
For the development of laminated cores for both the stator and the rotor, composite materials with high magnetic permeability and low loss such as Sheet Molding Compound (SMC), amorphous alloy materials, and oriented silicon steel are utilized. The SMC material has the characteristics of easy molding and simple heat treatment process, making it suitable for mass production. At the same time, due to its easy moldability, it can also be used in 3D printing technology to make the innovative design of motors more flexible and diverse. For the high-strength requirements of the stator and rotor, a carbon fiber winding fixation and reinforcement process has been developed to address the physical properties of permanent magnets that have poor tensile strength.
For the development of windings, rectangular-section copper conductors, helical concentrated windings, and multi-pole continuous winding processes are utilized. For the development of permanent magnets, low-loss segmented fixing installation and magnetic pole yoke demagnetization protection processes are implemented. For the development of stator cores, yoke-less segmented armature splicing and bolt-less fixed powder metallurgy manufacturing processes, which integrate with end covers, are developed. To meet the demands of batch production, automation assembly technology for stators and rotors has been developed, including automated production of flat conductor formed coils and flexible automated production line processes.
Investigate the mathematical models of the stator and rotor coordinate systems, construct a system simulation model, and study novel dual-vector model predictive torque control strategies to reduce torque ripple and enhance torque control performance. Focusing on the surface-mounted structure of the axial flux motor's permanent magnets, where the motor's quadrature and direct axis inductances are numerically very small, making vector control challenging and the magnetic circuit prone to saturation, develop control strategies to improve weak magnetic performance.
At Brogen, we're committed to offering custom EV solutions. We back these with new technologies to help EV companies thrive and promote environmental sustainability. Brogen provides an industry-leading EV Powertrain solution for commercial vehicles.
We've forged strategic alliances with key players in the new energy vehicle sector, including electric motor and controller manufacturers, battery pack producers, and charging station suppliers. We also collaborate with suppliers of essential components such as EV car battery, electric vehicle motor(PMSM motor), motor controller, OBC+DCDC+PDU, axial flux motor, BMS, air conditioning systems, air compressors, and power steering systems.
We have delivered high-quality electric powertrain solutions to over 100 customers across more than 20 countries.
Get in Touch with Our Experts
Are you interested in empowering your EV project? Reach out to our experts at inquiry@brogenmotors.com. We promise to get back to you within two business days.
For more videos please click Brogen’s Youtube.
For the latest news please view Brogen’s Linkedin.
Connect with a Brogen expert to learn more about our services and discuss our ePowertrain solutions.
Company Profile